Introduction
Industrial candle making machine factories are the backbone of a growing candle-making industry. They provide mechanized solutions to candle production, allowing for higher efficiency and faster production rates than by traditional methods. Industrial candle machines are large-scale, highly automated units that offer various types of molds, wax injectors and intricate designs that allow for the production of high-quality candles in bulk quantities.
The modern industrial candle making machine factory offers impressive levels of automation and customization which maximize productivity while ensuring quality control throughout the entire manufacturing process. The machines are user friendly, often equipped with intuitive displays that allow workers to quickly change parameters. This results in fewer errors, shrinking labor costs and greatly reduced training time. Furthermore, with advanced monitoring systems built into the machines’ software, any potential irregularities can be identified quickly and taken care of without interrupting production flow.
These cutting edge candle making machines also reduce materials waste by eliminating manual mixing processes which also helps to reduce costs significantly. Used together with independent weighing belt feedser machines this allows manufacturers to create more consistent batches that meet even the most demanding customer specifications while simultaneously lowering workforce requirements even further.
In short, an industrial candle machine factory provides businesses with a great solution for efficient and reliable mass-production needed for large orders or new product launches at scale on shorter timescales than ever before possible. With these tools now widely available it’s no surprise that some companies have already adopted such mechanized solutions as part of their core operations, leading to more successful projects thanks to improved efficiencies across almost every stage of the process.
Industry Overview
Industrial candle making machines have a long, fascinating history that can be traced back centuries. Early candles were probably made of dried organic materials such as animal or vegetable fats, rolled up in a cloth that would act as the wick. Over time, Beeswax began to take over as the preferred material with advances in technology enabling proper heat management techniques to produce effective and appealing designs from this material.
In modern times industrial candle making machines have become more widely available and used. Their increased usage has enabled consumers to enjoy beautifully-crafted candles for less money than ever before. They provide an avenue for businesses to create products quickly, without sacrificing quality and artistry. Additionally, these automatic machines are much more efficient than manual production methods and require fewer resources for manufacturing.
Modernindustrial candle making machines employ green technologies such as energy-saving lamps and air purification systems, thus reducing the amount of pollutants released into the atmosphere during their operation. Their use has also helped reduce electricity costs associated with manufacturing as they can run at optimal speeds while consuming less power compared to other machinery used in industry today.
Overall, these machines have had numerous positive impacts on the environment both locally and globally by providing low cost alternatives for creating unique candles while increasing efficiency and sustainability.
The Manufacturing Process
Industrial candle making machines are intricate pieces of machinery that have been designed to accurately and efficiently produce candles in large quantities. Candle making has been done for centuries, but today’s industry puts a lot into the production process in order to make it faster, more efficient, and more affordable to the consumer.
The manufacturing process begins with the selection of a wick that is optimized for each type of candle size, shape, and thickness. The wicks are then cut with precision using advanced laser-guided cutting equipment. They must be cut carefully as even the slightest variation can affect how quickly the wick burns through the wax.
Next, melted wax is poured into molds also produced by industrial candle making machines. This phase includes tinting and scenting of the wax if desired before it solidifies. After cooling, extra layers may be added in order to protect and decorate the candles according to their desired design. Once all layers are in place, they are sealed shut by melting them together once again.
The final step is packaging where each candle is checked for quality control before being boxed up ready for distribution. New technologies used by factories include 3D printing which allows for other shapes beyond candlesticks such as intricate figurines or flowerpots and AI/robotics which enables high speed production and customization within parameters decided by factory staff members.
Advantages of Utilizing Industrial Candle Making Machines
Industrial candle making machines offer a plethora of advantages compared to manual production processes. For starters, they are able to produce more candles in less time. As the machines are programmable and automated, the candle batch size can be easily adjusted, greatly boosting productivity. The quality of the resulting products is much higher due to increased consistency as well as repeatability of processing steps. Furthermore, employing industrial machines also ensures that your candles have consistent dimensions and shapes for each production run, thus giving them a professional finish.
The raw material costs for constructing a batch of candles can be reduced when using these types of machinery too, since wastage from the materials during assembly is much lower than with conventional methods. Many industrial candle making machines last longer than those used in manual productions due to their robust construction and use of high-grade components. Additionally, advanced safety features incorporated into the design helps prevent incidents during operation thus protecting both employees and clients alike. This results in higher customer satisfaction rates for your business over time as well.
Safety Practices
The Occupational Safety and Health Administration (OSHA) imposes or enforces safety regulations that must be followed when operating industrial candle making machines in factories. To comply with OSHA’s standards, all operators of these machines should be trained in their proper use and safety protocol, including the requirements for guarding, ventilation, electrical safety and housekeeping.
All machine guarding needs to be in place before the machine can be operated. The guards should cover all moving parts, to protect workers against the risk of being struck or crushed by them. Additionally, check for the presence of adequate ventilation during operation to ensure there is safe air quality free from dust and noxious fumes created from melted wax. Additionally, all electrical components must be properly insulated to prevent any contact with high voltage circuitry. Lastly, once a machine has been used, it is important to tidy up and reset everything prior to restarting it; this helps eliminate any potential hazards due to disorganization and clutter within an area where multiple machines are housed.
Regular maintenance practices are also essential for ensuring safe use of industrial candle making machines in factories. Regularly scheduled machine inspection not only extends the life of a machine but it also allows faults and malfunctions to be caught early on so they can be safely addressed in a timely manner before causing harm or injury. Common areas inspected should include blades or cutting tools which may become dull over time, mountings that may become loose or malfunctioning due to wear and tear over extended periods of time as well as any other moveable parts which could present a hazard if left unchecked. All findings should be documented for future reference in case additional repairs need to be made later down the line.
Industry Cost Analysis
Industrial candle making machines factories require a variety of components and resources to produce their candles. This includes the raw materials used to form the wick, wax, and other elements that are necessary components of quality candle making machines. Factors such as the size, complexity, and production capacity of the machine can have an effect on the overall cost of creating one unit. Along with this, companies must also consider what type of automation they need for their business to maximize efficiency. Automation may include features such as programmable controllers or robotic arms depending on what is needed for each type of machine. Additionally, various costs associated with powering the machines must be taken into account when analyzing industry cost for creating complete units. Often it is beneficial to examine any energy saving strategies available in order to reduce operational costs further down the line. Other costs can include research and development expenses related to designing new product features or software upgrades that may improve production rate or accuracy at work stations. After all relevant factors have been analyzed and calculated correctly, the details can be compiled into an accurate industry analysis highlighting costs associated with using industrial candle making machines in factories.
Future of Industrial Candle Making Machines
The future of industrial candle making machines looks very promising. With the advancements in technology, leading to the development of automated machinery and intelligent processes, it is becoming increasingly possible for manufacturers to produce high quality candles more quickly and efficiently. Automated machinery removes much of the traditional labor-intensive manual process associated with candle making and significantly reduces costs as well as production time.
With automated candle making machines, companies are now able to integrate advanced artificial intelligence (AI) technologies into their equipment which allow them to create candles that have higher standards in terms of color, shape, size and burn time. These AI systems enable the machines to rapidly adjust their manufacturing techniques according to the data found from a sample of recent products or even from consumer preferences. This allows companies to further refine their candles both in terms of speed and quality.
In addition to these advancements in intelligent automation, Industrial 3D printing technology is also revolutionizing the candle making industry with smaller batch customization or short run personalization becoming less costly and practical. This revolutionary process greatly reduces production costs since tools can be made on demand rather than having mass produced tupperware molds shipped in bulk across continents for each project. It enables faster design iterations for each project allowing for quicker prototyping followed by rapid production turned around periods once desired results are achieved without any compromise on plastic parts quality or finish options.
Conclusion
Industrial candle-making machines offer a variety of benefits to companies wishing to produce high-quality candles in higher volumes. This type of technology allows companies to increase their production efficiency, resulting in lower costs and faster turnaround times. Utilizing industrial candle-making machines also provides increased safety protocols when dealing with molten wax, ensuring that no safety hazards arise during the manufacturing process. In addition, these machines allow for a greater level of quality control since they are designed to ensure consistent shape and size for each candle produced. Companies can also further optimize production through adjustable settings that optimize the burning time of each individual candle. All in all, utilizing industrial candle-making machines provides an array of advantages and helps companies increase production while minimizing costs and optimizing the quality of their product line up.
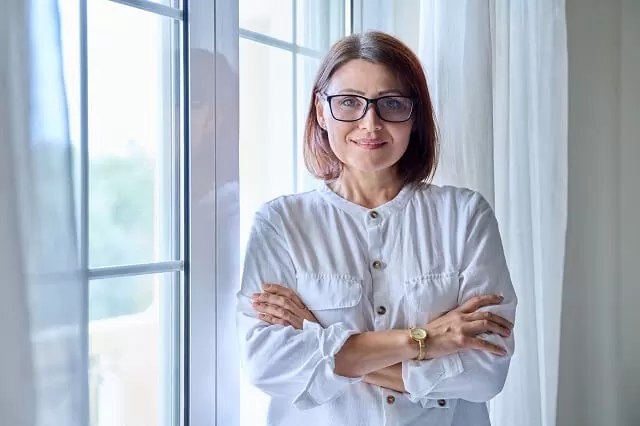
Welcome to my candle making blog! In this blog, I will be sharing my tips and tricks for making candles. I will also be sharing some of my favorite recipes.