Introduction
Automatic candle making machines are specialized machinery that facilitates the production of candles from wax and paraffin. These machines offer manufacturers a cost-effective and automated approach to the production of candles in large quantities for a variety of applications. Automated candle making can be used to create candles for religious ceremonies, memorials, aromatherapy, lighting, and decorative purposes.
The particular type of automated machine used is dependent on the desired output. Generally, automatic machines make use of a combination of conveyor belts, extruders, and injection systems to precisely measure and shape molten wax into pre-programmed sizes and shapes. Common machine types include single or double colour wax injectors, manual tin dipping machines, vertical rotary pulling machines, liquid drip line filling machines, perforators (with which wicks of varying length can be accurately positioned), electric sealers (for coating candles with metal foil) and form fill & seal wrappers (which package candles into pre-cut cellophane). Ancillary equipment such as die cutters may also be used in certain manufacturing processes.
History
Automatic candle making machines have been around since the mid-1800s when they were first used in the United Kingdom and United States. Originally, these rudimentary mechanical machines were used to roll candles out of wax sheets. In 1867, U.S. Patent Number 71,092 was issued for the first “mould-and-press” process of candlemaking, machines that used heat to melt and mold multiple candles at once.
By 1900, a pneumatic system for candlemaking was evolved in America by a Joseph O’Neil which made it possible to blow molten wax into various molds and designs. This modernised the entire industry, reducing labor costs dramatically and allowing for much more intricate and creative shapes to be produced. The next big technical advance came in 1935 when Robert Davis developed the vertical injection method which allowed for far higher output levels as well as near perfect production accuracy as supplies could now enter from any direction instead of just one side (as with pneumatic machines).
From 1952 onwards further refinements began to take place even though the basic technology had remained unchanged since O’Neil’s inventions of sixty years prior. Machines with increasingly automated capabilities were developed such as nozzles that operated without human staff needing to be in attendance although this was still somewhat limited due to lack of suitable technology at the time. With more advanced computers and robotic automation becoming commonplace in factories from late 1960s onward gradually saw leaps forward being taken giving rise to fully automated plants that are able operate on their own today with minimal staff required.
Production Process
The production process for automatic candle making machines consists of a number of assembly steps to construct the machine. The parts are typically sourced from multiple suppliers, including raw materials and components. First, the body is constructed which includes an aluminum alloy frame and steel handle. This includes cutting, drilling and milling the metal components. Then, two motors with variable speed control are added to the base plate of the machine. Afterwards, a heating chamber is constructed with ceramic materials for melting wax and a temperature controller that regulates heat automatically. The bottom of the machine is fitted with wheels for easy transportation between production stages. Next, electronic switches, motors and other associated components are added to run the various mechanisms involved in candles making machine operations. Finally, safety features such as fireproof insulation panels are installed for extra protection against any unexpected accidents which may occur during operation. After all components and parts have been properly assembled and tested for quality assurance by technicians, the finished machines are shipped to customers worldwide.
Types of Machines
The automatic candle making machine factories produce a wide range of machines designed for specific candle making processes. Depending on the manufacturing complexity and intended purpose, these may include wax melting machines, mixing and dispensing systems, wick feeders, molded candle presses, cooling tunnels, labeling machines, and packaging equipment. In order to create multi-colored candles or candles with gradual shades in one production cycle with different colors of waxes and dyes, factories can use special machines with dye injection systems. This system is designed for cold-processed production lines that allow for precise application of colored wax or immersion into the wax at calculated speeds. The machines can also be equipped with special nozzles to facilitate embedding decor elements such as jewel dusts or glitter into the melted wax. For product safety reasons these decoration elements should not be emitted from the device until they dissolve in hot liquid wax due to their potentially hazardous nature. Other types of automatic candle making machines include scented oil injectors which are designed for adding fragrance oils during production cycles as well as top printing devices used to apply intricate patterns on surfaces during cooling periods. These systems may feature automated control programs which regulate temperature according to type of product in order to ensure optimal levels of performance.
Automation
Investing in automatic candle making machines is a great way to boost productivity and efficiency. Automation can help streamline the entire production process, from initial design to finished product. It eliminates manual labor, reduces waste, and increases overall efficiency.
Manufacturers that upgrade to an automated system will be able to produce high-quality candles in shorter timespans. This can be especially helpful for manufacturers who are trying to enter new markets or trying to meet customer demands with tight deadlines. Automated systems allow for easier customization of candles which helps companies better differentiate themselves from competitors and provide more customer-specific options.
The accuracy of automatic candle making machines also ensures consistent output with each production run, reducing waste and improving the quality of candles produced. As automation takes over many different parts of the manufacturing process, the risk for human error is drastically reduced as well. With fewer mistakes made during the production stage, companies have an easier time creating a reliable product with a minimized chance of receiving returns or complaints from consumers unsatisfied with the quality of their purchase.
In short, investing in automated candle making machines provides numerous benefits in terms of efficiency and quality control while reducing overhead costs associated with manual labour and human error. Manufacturers that upgrade to an automated system will see significant improvements in their ability to develop customized candles quickly and consistently that meet customer demands.
Safety
The safety of those who work with automatic candle making machines is of utmost importance. Therefore, all industrial factories (and others who are involved in manufacturing candles) must ensure they implement appropriate procedures and precautions to protect staff working with the machines. All employees should receive specific training and continued education in safety protocols related to the machine. Before using any machinery, it is important for each user to become familiar with the equipment as well as follow any rules or regulations regarding use. Additionally, wearing protective gear at all times is a must, including high-visibility clothing and gloves when handling material, as well as goggles and other equipment for protecting eyes. Additionally, regular maintenance checks should be made on the machines to make sure that there isn’t any damage or malfunctioning which could put employees in danger. Finally, ergonomic furniture and equipment such as adjustable chairs and keyboards should be provided in order to reduce instances of musculoskeletal injuries due to prolonged periods of standing and sitting. With these procedures and precautions in place, workers can be sure that they will remain safe when working with automated candle making machines.
Factory Layouts
Factory layouts vary from business to business, depending upon the type of product being manufactured. However, depending on the type of factory, there are generally three main types of factories: batch production factories, assembly line factories, and automatic candle making machine factories. Batch production factories create a large amount of different items over set periods of time and require minimal changes in machinery or workers as products change. Assembly line factories produce items in a continuous flow by breaking down the steps into distinct tasks to be completed one after another. Finally, automatic candle making machine factories are often used for specific applications such as producing scented candles and homemade wax candles; they use unique machines that automate most of the production process.
Factory layout is determined by the size and shape of the factory site and other environmental factors such as traffic, government regulations and customer demands. For example, some batch production factories are designed to have multiple workstations with multiple workers stationed in each station while others are designed with a single worker completing tasks in sequential order at each station. In an assembly line factory, machines and automated systems need to be arranged in a coordinated chain from point A to point B with little disruption between them. Automatic candle making machine factories require specific machinery and conveyor lines that must be organized for optimal efficiency and cost savings. Additionally, factors like lighting design and ventilation must also be taken into account both for safety reasons as well as employee satisfaction due to long hours spent working inside the factory environment.
In addition to determining efficient layout designs for each factory type based on physical factors like size considerations, managers must also factor in personnel needs when designing their layout plans, allowing for access to resources like ergonomically-designed chairs or adequate restrooms throughout their facility if needed. Alongside this, floor markings can help staff easily differentiate between walkways intended only for foot traffic while storage areas can help organize shelves filled with materials more efficiently within a factory setting; once established it helps reduce unnecessary movement when fulfilling orders quickly or finding specific parts needed during production processes easier day-to-day too! As technology advances, many different types of robots can now contribute to assembling products easier than before–ultimately resulting in fewer personnel requirements” -allowing plants to become more streamlined at higher speeds than ever achieved before!
Efficiency
Automatic candle making machines are significantly increasing the efficiency of production in factories worldwide. Automation is reducing labor costs and permitting uniformity in product output, resulting in mass-produced products at much lower prices than ever before. The introduction of machine automation into general manufacturing processes has resulted in sizable productivity gains, allowing for higher levels of customer satisfaction.
Gains in efficiency have enabled factories to meet customer demands at faster rates and lower costs than ever before. Through the use of automated machinery, companies can provide better quality candles with a greater degree of consistency since machines can ensure that each candle is made according to specified criteria. Additionally, these systems also allow lighten or shorten up production times and result in reduced waste due to the precision given by an automated system monitored by a workers throughout the entire process.
Moreover, these automated systems have also allowed for constant monitoring and control over the production process. Automated systems feature enhanced safety protocols that enable more secure operations by removing hazardous components from the production chain, reducing risks posed by human error and creating a safer working environment for employees. All of these variables combined create an ideal setup for factories manufacturing candles using automatic machines. Ultimately, machine automation has revolutionized candle making factories from coast to coast with greater efficiency and higher productivity, expanding their capabilities and allowing them to generate larger quantities more quickly with fewer resources than before implementation of robotic systems.
Cost of Manufacturing
The cost of manufacturing automatic candle making machines depends on a lot of factors, such as material and labor costs, technical specifications, production capacity, quality standards and the demand for the product. Material costs are often the highest expense involved in producing these machines. The purchased metal parts need to be processed, find their appropriate place and then welded together. Primarily, stainless steel or aluminum are used for a high- quality output of the finished product. Furthermore, labor costs must also be taken into account when assessing all necessary expenses. Tens or hundreds of professionals who specialize in mechanical engineering usually develop the blueprint designs for these machines and help to bring them to life. Technical specifications also differ according to the customer’s needs; certain companies require higher levels of efficiency than others which affect production rates as well as resulting in more costly equipment. Similarly, varying levels of production capacity require more energy consumption and an increased number of manual labor hours needed for completion – this can add up quickly in terms of expenditures that need to be budgeted for. In addition, specific quality assurance regulations must be followed in order to meet requirements mandated by industry standards; this directly impacts associated expenses related to safety features incorporated into each machine’s design before it’s released onto the market. Last but not least, demand will heavily influence how much money is spent on building these candle making machines; In times of peak commercial demand prices may surge due to an increase in orders coming through different channels such as online retail stores or international shipping outlets. Allowing a proper margin for unexpected delays/supply chain disruptions is essential if one intends to keep long-term profitability goals intact at all times throughout the entire process.
Future Developments
Automatic candle making machine factories are an important part of the candle industry due to their ability to mass-produce candles with consistent quality. As technology advances, there is potential for greater improvement and innovation in automatic candle making machines. For example, 3D printing has the potential to create more intricate designs and shapes when it comes to candle production ” something that could be largely beneficial for businesses that specialize in custom scents and designs. Additionally, developments have been made in terms of lighting sources, such as LED-based solutions, that could make an automated process more energy-efficient. In addition, machine learning algorithms could be utilized to reduce waste and maintain various batches of candles identical in appearance or smell ” modifications that would lead to cost savings for production companies. Finally, advancements such as computer vision hardware improvements may potentially enable machines with greater accuracy when creating complex patterns both safely and quickly. All these proposed modifications could lead to a new generation of efficient and reliable automatic candle making machine factories.
Conclusion
The introduction of automatic candle making machines in the industry has proved to be extremely useful. This type of automated equipment has improved workflow, increased production, and decreased labor costs for many businesses in the candle-making sector. Additionally, automation has enabled corporations to increase the quality of their products and reduce variation by improving uniformity of output. Moreover, with reduced manual work, health and safety risks associated with working with molten wax have been minimized. Therefore, it can be said that automatic candle making machines are invaluable tools in the industry which have brought about a revolution in productivity that could easily have been missed without their presence.
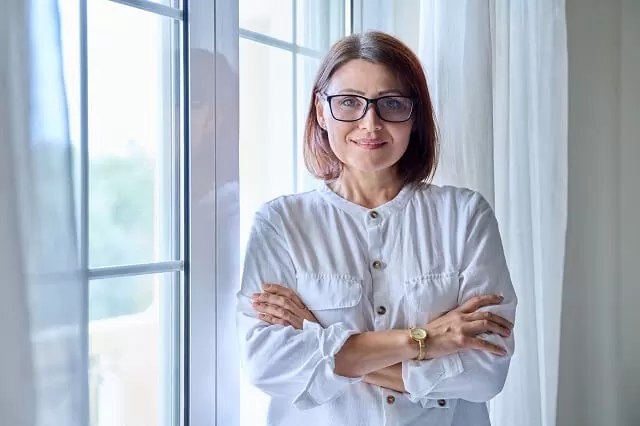
Welcome to my candle making blog! In this blog, I will be sharing my tips and tricks for making candles. I will also be sharing some of my favorite recipes.