Mold making is a creative process of forming hollow or modified shapes with various materials, especially using plaster of Paris. It enables you to custom design shapes and sizes for candle production or any other applications. The best mold making material for candles should have characteristics that allow the casting of molten wax without compromising the details and designs in the molding. Mold making can also save time and money when producing multiple, identical products.
Types Of Mold Making Materials The most common materials used in mold making are silicone, latex, rubber molds, metal and plastic when casting candles. Silicon molds are easy-to-use, long lasting and flexible enough to keep the shape of the poured object intact while still releasing it quite easily after cooling.
Latex molds are a cost-effective option but need specific upkeep to prevent premature aging from sun exposure and regular washing with dish soap or mild detergent solutions to also keep them from sticking product over time.
Rubber molds also provide similar results as silicon but creating intricate shapes due to their low elasticity can be more difficult task with it then silicon molds. And melting plastics belong in last category as they are prone corrosion, require extra preparations when pouring wax into them while being relatively heavier than other options which make them difficult to work with.
Choose The Best For Your Casting Needs When choosing the best material for mold making for candle or wax casting applications, silicone is usually the go-to option due its flexibility attributes and ease of use even on complex designs or intricate detailing. It is heat resistance, non-toxic and can be used multiple times since it’s durable enough to handle many repeat uses across different temperature ranges without negatively affecting its structure or performance.
Its durability is ensured by vigorous testing during production ensuring optimum performance every time it’s used resulting in quality results suitable for both amateur projects at home or professional productions at larger scale businesses catering more demanding needs in terms of details and design features expected from quality products meeting industry standards.
Different Types of Material Suitable for Mold Making
Mold making for candle making is an important step during the process, as it affects the size, shape and end look of the candle. The best type of material to use depends on the design desired and the budget available. Popular materials used in mold making for candles are plastic, metal, silicone, plaster and wax.
Plastic
One of the most commonly used materials for candle mold making is plastic. Plastic molds are usually less expensive than other options, and they offer better flexibility as they can be shaped into a variety of patterns.
Plastic molds can also be reused multiple times without losing their shape or durability. However, as wax has a tendency to adhere to plastic molds, it is advisable to coat the inside of them with a layer of petroleum jelly or cooking oil before pouring your wax into them.
Metal
Metal molds are most popularly used for making pillar candles where intricate design details are desired. These types of molds are durable and sturdy compared to plastic molds, making them ideal when working with large volumes of molten wax or heavier pieces like jars. Metal molds require some preparation time as they should be coated with petroleum jelly to prevent sticking before pouring in any molten wax.
Silicone
Silicone is another popular option for mold making which has grown in popularity due to its user friendly properties such as low cost, lightweight and flexibility (can produce intricate details). It’s also temperature resistant so hot wax will not cause any damage to it which allows larger batch production with ease and quality output when compared to other materials mentioned above.
The only negative side to using silicone mold is that after repeated uses it may lose its shape (particularly if exposed to extreme heat).
- Plastic: less expensive than other options; can be shaped into different patterns; needs coating in between uses.
- Metal: Used for pillar candles; Sturdy & durable; requires coating before pouring.
- Silicone: Quite user-friendly; Temperature resistance; Can lose its shape after repeated usage.
Advantages of Silicon for Candle Molds
Silicon is widely regarded as the best material to use when making molds for candles. It possesses several qualities that make it suitable for candlemaking, including durability, flexibility and temperature resistance. On top of this, silicon is relatively inexpensive and can often be re-used multiple times.
Durability
Silicon molds are generally very durable and resistant to wear and tear, which makes them an ideal choice for candle making. Unlike more fragile materials such as metal or plastic, silicon molds won’t degrade over time with repeated use.
The fact that they are flexible means that they can handle the higher temperatures which are generated during the candlemaking process without buckling or melting. This mean that you don’t have to worry about replacing your molds too often due to damage – which makes this type of mold both economical and efficient in the long run.
Flexibilty
Silicon molds are highly flexible and easy to manipulate. This enables you to easily pour hot wax into the mold without having to worry about spillage or air bubbles forming in the mould cavity. Furthermore, since silicon is a pliable material you are also able to twist and bend it without risking any damage being done – something which you wouldn’t be able to do with rigid materials such as wood or metal.
This flexibility also means that if you need to remove a stubbornly stuck candle from its silicon mold then this can usually be achieved by simply twisting and bending the mould slightly in order loosen its grip on the article inside. This helps ensure that your candles will remain intact despite them being subjected to some force during removal from their moulds.
Temperature Resistance
Silicon is able to withstand temperatures ranging from – 104°F up to 446°F without any appreciable degradation – meaning it can easily cope with even extreme heat sources such as boiling water baths used in some types of candle crafting processes (such as container candles). Its high melting point therefore ensure that your finished product will not suffer discoloration due heat transfer from hot wax into its moulds during manufacture.
Selecting the Appropriate Mold Material for Your Needs
Candle making is both a popular pastime and profession for many people around the world. Whether you’re just starting out or an experienced artisan, selecting the right mold material for your job is essential.
While there are several materials suitable for use in molds such as silicone rubber, polyurethane, epoxy resins, gypsum-based plasters, and others; there are some that stand out among others when it comes to creating the perfect candles. Here are some of the best mold making materials for candles:
- Silicone Rubber – Silicone rubber has a temperature tolerance that allows it to withstand successive pourings of hot wax without damaging under high heat. This makes it one of the best materials for candle molds since it will retain its shape even after pouring multiple times.
- Polyurethane – Another excellent choice when it comes to molds for candles is polyurethane. It can be easily molded into any shape or size due to its malleability and though not as durable as silicone rubber; it still offers superior performance when used at moderate temperatures.
- Epoxy Resin – Epoxy resin holds up well against high heat and can also be poured multiple times so that you can make several types of designs with the same mold. It has also been found to be less prone to cracking which makes it ideal for more intricate patterns.
- Gypsum-Based Plasters – Gypsum-based plasters have been used in candle making for centuries and offer excellent long-term stability in terms of heat resistance and wear resistance. They are also able to accept various dyes used in candle making without discoloring or affecting their durability.
When selecting a mold material, keep in mind what type of candles you plan on making because this will determine which material is best suited for your project. Materials with higher heat tolerances should be chosen if you plan on using hot wax while more flexible options should be chosen if you prefer liquid waxes.
Additionally, taking into consideration how often you plan on using your molds may help narrow your selection down further based on maximum number of uses and ease of care required after each pour. With all these factors taken into account; you’ll have no trouble finding the perfect mold material to create beautiful candles with.
Step-by-Step Guide to Creating a Candle Mold Using Silicon
Having the right materials on hand is essential when making your own candle molds. Before you start the process, it’s important to consider the best mold making material for candles. One popular option for this task is silicon; its flexibility and non-stick properties make it an ideal choice for easy removal of the final product. Below is a step-by-step guide to creating a candle mold using silicon:
- Clean and prepare your work area: Make sure your work area is free from dust and debris by wiping down your surface or grabbing a lint roller to remove any potential buildup.
- Measure and assemble mold material: This step requires careful measurement so be sure to accessorize with measuring tools including rulers and/or tape measures. Once measured, assemble all pieces of need hardware into one cohesive piece.
- Add sealant or fastening agent: Using sealing agents such as glue not only provides extra stability but helps protect against corrosive elements like water.
- Mix together the silicon rubber compound: Before pouring into molds, mix the content thoroughly until it becomes malleable.
- Pour into molds, wait for hardening: Do this slowly as pouring too quickly could possibly displace your hardware. Leave room for volume expansion while in use before allowing it to harden.
Once dried, carefully remove from molds and use as desired. To ensure easy removal of candles already formed without being damaged afterwards make sure that prior preparation is done in advance including adequately waxing, greasing or sealing off all surfaces within molds accordingly.
Molded candles should always be used with caution due to their different characteristics such as fragility; so handle with care when burning them inside specially prepared areas (such as heat resistant containers). Lastly, storing candles in suitable dry places away from direct sunlight can further extend their lives.
How to Care and Maintain Silicon Candle Molds
Silicon candle molds are currently the best mold making material for candles available on the market. Silicon has long proven to be an excellent choice for candle molds, even taking into account its relatively high cost.
It’s extremely durable, resistant to heat and able to withstand the wax filling with no leaking or cracking of the wax form, resulting in beautiful and highly detailed candles that maintain their shape. Being non-stick it is also very easy to use and release products from the mold as soon as they’ve been casted.
It’s important to take care of silicon molds when creating your candles – there are a few steps you should take in order to ensure your mould lasts as long as possible. Firstly, you should always use a mild detergent – one specifically formulated for silicone is ideal – and never immerse the mould in water or any other liquids; this could safely ruin it over time due to deterioration of the material over time.
Secondly, you must make sure that which ever wax you are using for your candles is at an appropriate temperature before pouring since too hot of temperatures may damage it.
As well as storage after a session of pouring candles in silicon molds, cleaning should also be considered an important step in caring for them.
To properly clean a silicon mould start by wiping away any leftover surface debris with either a dry cloth or brush – then using your mild detergent create a lather on top of this before rinsing off all soap residue completely (these steps can also be followed if the mould has endured intense use or high temperatures).
Finally finish off with drying using either an absorbent cloth or air-drying at room temperature, ensuring the mould does not come into contact with extreme humidity or direct sunlight while doing this so as not cause further damages to it. Following these steps will help keep your silicon candle molds looking good and performing their job perfectly each time.
Tips and Tricks for Extracting the Candle From the Mold
For those looking to make a perfect candle with beautiful detail, the best mold making material is silicone. Silicone has excellent casting qualities and allows for easy extraction without damaging the candle.
It’s a great choice when creating intricate and detailed candles, as it creates an even heat distribution while also providing release ease. Despite other materials such as glass, metal or plastic being cheaper options in some cases, they do not provide the same kind of release that silicone does.
When taking any candle out of its mold, proper safety and caution should be taken to avoid damages such as breakage or burning resulting from too much contact with the heat or flames from the candle itself once lit. The first step before extracting is to make sure that the candle has cooled off completely, letting it sit until may take about an hour if left undisturbed.
For further ease in extraction, using two butter knives is very useful when prying open the sides of a silicone mold – this helps pulling away any remaining bits that may have stuck together during hardening process.
Apart from cooling off the candle before extraction, temperatures can also be manipulated while still inside the mold. By lowering the temperature slightly when pouring molten wax into many ports on a silicone compounds helps promote an easier extraction process; instead of having to rely solely on cooling for removal without breaking sections.
Another trick is using a hard tool like a spoon handle tap around gently to free up and glue any parts that may be fused with each other thus preventing splitting of pieces upon removal from the mold itself. Such techniques are beneficial to creating extremely detailed candles in terms of form factor but most importantly ensuring there is no damage caused to the outer layer during extrusion.
Summary
When it comes to making candles, the mold-making material is critical for achieving optimal results. There are several types of materials commonly used to make molds for candle casting, and each type presents its own unique advantages for working with candles. The most popular options include silicone, plaster, wood, and non-stick plastic.
Silicone is often regarded as the best option when making a mold for candle casting due to its flexibility and ability to hold intricate detail well. The material is also very durable and has good heat resistance, so it will be capable of making multiple successful casting cycles before needing to be replaced. Additionally, silicone molds can range greatly in complexity and allow users to create more elaborate designs with minimal effort compared to traditional plaster or wooden molds.
Plaster is also a popular choice as it produces adurable mold that can form excellent detail but not on the scale possible with silicone. Plaster also provides great insulation which keeps heat from transferring through too quickly while hot wax is poured in – ideal for a slow pour and a smoother end product – but does have less resistance to thermal shock than some other materials on this list.
Wooden molds are lightweight and versatile but require extra layers of protective wax or glaze prior to pouring hot wax as they deteriorate quickly under extreme temperatures.
Non-stick plastic molds offer an affordable solution with an impressive level of detail but these materials can’t withstand extremely high temperatures without warping or melting over time. Furthermore, they are known to produce lower quality results when compared to silicone or plaster – ideally suited for experimenting with new shapes or sizes rather than producing professional quality castings.
Ultimately, it will depend on what aspects of the crafting process the creator cares most about when deciding which material will suit them best in their project endeavors.
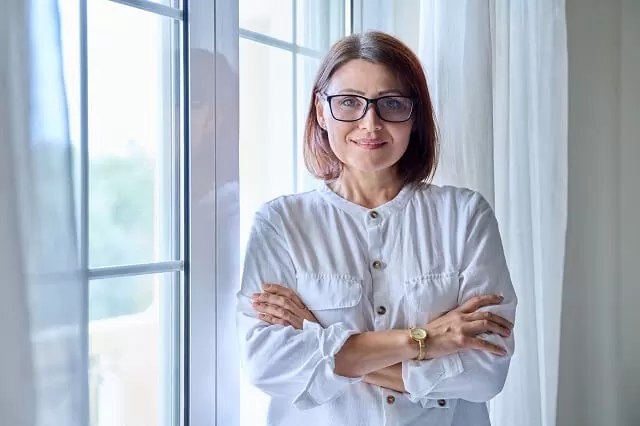
Welcome to my candle making blog! In this blog, I will be sharing my tips and tricks for making candles. I will also be sharing some of my favorite recipes.