Introduction
Candle making inventory is an important part of any candle business, as it helps to ensure that you are able to track your materials and able to put together a professional product every time. It can be difficult work to keep everything in order when you are creating candles by hand, so having a well organized inventory system in place will make your life much easier. An inventory system should include all the necessary materials you will need for each candle type and project, such as waxes, dyes, fragrance oils, wick supplies, containers or molds. You should also always keep records of how much of each material is left in stock and how many candles have been made with it. This makes it easy to purchase and restock the necessary supplies for future orders or projects. Additionally, by keeping track of what ingredients are needed for each candle or melt recipe you create will save valuable time and help to maintain consistent results from batch to batch. Overall, having a solid candle-making inventory management system in place will allow you to easily manage your materials while creating beautiful products that are sure to please!
What to Track
In candle making businesses, tracking inventory is an essential part of maximizing profits. Many items should be tracked in order to know what has been sold and what needs to be replaced. This includes the wax, dye, wicks, fragrances, containers and accessories that are used for creating different types of candles. Additionally, it is important to track the tools such as thermometers or melting pots that are used to help with the production process. Not only should these items be tracked but the amount of each item in stock should also be monitored and regularly replenished when necessary. Keeping accurate records of all candle making materials will help prevent running out of vital supplies, thereby avoiding costly delays in fulfilling orders and maximizing profits.
Data Entry Tips
When tracking candle making inventory, it is important to create a system that helps you effectively record and monitor changes. Developing best practices when entering data can go a long way in ensuring accurate records and preventing costly mistakes. Here are some tips to help you with your data entry process:
1. Use consistent formatting ” Creating standardized templates for data entry will help keep things organized and ensure accuracy across the board. It can be helpful to break up product information into different categories such as name, description, units of measurement, expiration date etc., or to utilize predefined input templates from software programs.
2. Double check data ” Once you have completed your data entry, review the information again to make sure all details were entered correctly before finalizing your records. If information is missing or incorrect, take the time to make corrections on the spot instead of waiting until later.
3. Organize information ” Utilizing folders and labels can help streamline the data entry process by allowing you to easily locate what needs to be entered or updated without having to search through cluttered spreadsheet rows and columns.
4. Establish guidelines ” Outlining customized procedures for each type of transaction your business encounters can guarantee more efficient workflow processes throughout the various stages of inventory tracking; setting target completion dates helps maintain accountability while adjusting parameters accordingly prevents overspending or mistakes due to manual error.
5. Regularly back up files – When keeping track of critical business records such as inventory tracking data, it is important to regularly store backups offsite in order maintain continuity no matter what happens locally on your computer system
Advantages of Tracking
Having an accurate inventory tracking system for candle making supplies can be extremely beneficial. Not only does it save time and money as you can keep a precise record of your inventory, but it also offers greater efficiency in a variety of ways. An accurate tracking system helps to identify patterns in purchasing habits and usage, allowing you to better manage costs associated with production while monitoring output levels. It also provides the ability to anticipate demand ahead of time and ensures that the materials needed are always on hand when required. Knowing exactly how many items you have means no unnecessary over-purchases or overstocking which would result in lost capital and financial losses. Finally, having an accurate inventory keeps your business running smoothly as you are able to easily identify what is available at any given moment, keeping production on schedule and customers satisfied.
Strategies for Inventory Control
One strategy for ensuring inventory control is implementing a system for tracking inventory levels. This may include regularly monitoring the number of candles and other products in your inventory, noting when you need to reorder supplies, and making adjustments accordingly.
Another important strategy is to develop safety procedures such as storing flammable goods safely and securely. This could include installing smoke detectors in areas where candles are stored, placing signage indicating fire safety protocols, and employing individuals who are trained in safe candle-making practices.
In addition, it is essential to have appropriate storage practices in place. This could involve creating a system of shelves or bins that clearly indicate the type of product and the quantity available so that refilling stock can quickly be identified. It may also be beneficial to label products with expiry dates to avoid having surplus goods take up valuable storage space or unexpectedly become unusable due to spoilage.
Finally, if applicable, consider using technology to further streamline your inventory control process. Automated order systems can increase efficiency by automating low stock notifications and generating sales forecasts based on past purchases. Intelligent software systems that analyse trends can help anticipate future customer demand and provide better insights into when you should plan additional orders or promotions.
Automation for Inventory Management
Automation is becoming increasingly essential for inventory management. Through automated software, organizations can keep a real-time account of the items they need to track, including those related to candle making. By automating processes and tracking methods, businesses can better manage their inventory in ways that are more efficient and effective than before.
Inventory automation can help prevent errors and ensure that all aspects of the inventory are accounted for accurately. Automating transactional processes also eliminates much of the manual labor associated with traditional methods such as physical counts which can be time consuming both in terms of personnel needed as well as duration. Automation also helps anticipate upcoming shortages so measures can be taken to replenish stock as required. Companies employing automation tools also benefit from increased efficiency, by studying past usage trends along with customer-demand data which can help offer optimal recommendations for reorder points before running out of stock. The one disadvantage is the higher initial costs of automation compared to manual methods but these provide long term returns on investment for areas such as process optimization and cost savings on labor.
Documenting Transactions
Keeping accurate records and documenting all business transactions is important for any candle making business. This ensures the accuracy of financial statements, invoices, revenue tracking and other essential accounting processes. It also allows owners to keep track of their inventory levels, identify what ingredients have been used, analyze customer trends and plan effectively for the future. Documenting each transaction also makes it easier to spot suspicious activity like theft or fraud in the case of any discrepancies that may arise from sales and expenses.
Accurate record-keeping reduces the risk of both internal and external errors when preparing annual reports. It also eliminates confusion about procedures by providing clarity about protocols for ordering supplies or contacting vendors. Additionally, a systemized documentation of all transactions enables owners to calculate taxes more accurately and helps prevent losses due to inflation or general market changes that might occur over time. Furthermore, having a secure filing system is helpful in case auditors decide to review the company’s fiscal records at any given time.
Having a solid inventory management system also benefits candle making businesses in many ways. Businesses can use it to understand their customers’ buying behavior more accurately by keeping track of which products are selling quickly and those that are slower movers. In addition, being able to manage inventory levels more efficiently boosts customer satisfaction as businesses are better able to anticipate shortages or restocking needs when needed ” meaning customers can purchase what they want without worrying about possible disruption in supply or stock availability due to miscalculation or miscommunication between various parties involved in production Chain supply. Finally, businesses can use accurate records to develop powerful marketing plans based on the data they hold such as hours when they’re busiest or even daily foot counts ” all essential elements towards ensuring an ongoing success within the industry today
FAQ on Candle Making Inventory
Q: What does a candle making inventory consist of?
A: A candle making inventory typically consists of a list of all the materials needed to make candles like wax, dyes, fragrances, wicks, molds, containers, and any other necessary supplies. Additionally, some additional items that may be included in an inventory include tools such as double boilers and thermometers as well as finished products.
Q: How is the candle making inventory tracked?
A: The primary way to track a candle making inventory is through spreadsheet or database programs like Excel or Access. Manual processes may also be used depending on the size of the operation. Using a digital approach makes it easier to keep track of current inventories and updates can be made quickly and accurately.
Q: Is special software required to manage a candle making inventory?
A: Not necessarily. While special software designed for tracking inventories may be used, there are also plenty of options out there that don’t require any specific type of software and are just as effective. It really depends on your needs and how much detail you would like your records to contain.
Summary
Having a detailed inventory list for both supplies and finished products is essential for successful candle making. Keeping track of not only the material and supplies used in making the candles but also their corresponding costs, quantities, open orders and any other relevant information can help ensure that you have enough of each component on hand to meet production needs, while maintaining an accurate understanding of your overall cost to produce. With this organized list and data readily available, you will be able to accurately gauge how much profit you are generating per product sold and how best to optimize your candle-making process. Keeping track of an up-to-date inventory list with all pertinent data points is crucial in order to successfully run a candle making business.
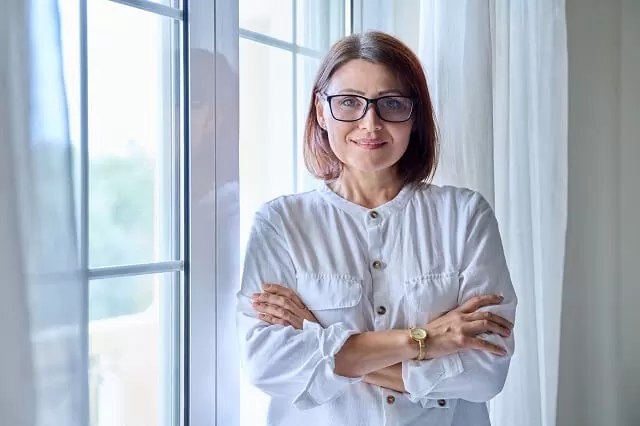
Welcome to my candle making blog! In this blog, I will be sharing my tips and tricks for making candles. I will also be sharing some of my favorite recipes.