Introduction
Project cost for candle making is the total sum of money needed to start a candle-making business. It is important because it indicates how much financial resources are required in order to successfully produce and market your candles. This includes costs for materials, tools and equipment, labor, insurance, marketing efforts, taxes, licenses, and other charges. Knowing the project cost beforehand can help ensure that you stay within budget once production steps up and that you do not run into unexpected expenses down the road. It can also help to provide information on cash flow so that you manage your money wisely during all stages of production.
Materials
The materials needed to make candles are wax, wick, fragrance oils, a thermometer, and molds. Depending on the size of candle being made and the type of wax being used, the amount of wax needed can vary. Wick needs to be selected carefully as it will determine how the candle burns; you should look for a wick that is appropriate for the size of the candle and for the temperature at which it will be burned. Fragrance oils are necessary if you want to make scented candles; choose from among a variety of fragrances available online or in craft stores. A thermometer is important for melting down wax properly without burning it. It is also important to make sure that the molds you use to form your candles are made with food-grade materials so they won’t contaminate them or release toxins when heated.
Costs of Materials
When making candles, it is important to consider the cost of materials when making budgeting decisions. Generally, there are four main materials involved in candle making: wax, wicks, dyes or colors, and fragrances.
The cost of wax varies greatly depending on the type of wax you choose and where you source it from. For example, purchasing beeswax can be more expensive than paraffin or soy waxes, however beeswax often offers superior burning quality and a longer burning life for your candles. It is important to research the various types of waxes available and determine which type works best for your project needs before purchasing supplies.
The cost of wicks also varies depending on their type and size, which ultimately depends on the size and shape of your candle. A wick must be large enough that it produces no smoke while burning properly but small enough that it won’t draw too much melted wax down into the container if placed too deep in a candle. Generally, natural or uncored cotton or hemp are popular alternatives as they are easy to use and provide good performance in terms of burning properties.
Dyes add color to your candles but may be unnecessary depending on the desired look and usage. For instance, some may want colored tealights or scented pillar candles while others prefer neutral-colored votives without scent or coloration at all. For those who opt for dyeing their candles though, research what type of dyes are suitable as some may not fully dissolve in molten candle wax. Prices will vary based on brand name and quantity purchased so evaluate different suppliers carefully before committing to a purchase decision.
Finally, decorative fragrances are available to add additional scent enhancement to candles but likewise tend to come at a higher price tag than other materials used in candle making. Though expensive compared to other supplies used for candle making, fragrances may prove invaluable when creating custom scented creations that give off strong yet pleasant aromas upon burning which makes them worth considering if desired within a given project’s budget parameters.
Labor
Labor is often one of the most important variables when it comes to calculating project costs for candle making. Depending on how many candles you plan to make, the hours of labor required and company’s hourly rate all need to be considered when estimating labor costs. If the candling process is done by an individual or a team, rates can vary greatly between different companies and the cost of labor can significantly affect overall costs. The cost of labor should be estimated based on the number and types of candles being made as well as necessary materials, equipment and supplies associated with each step in the candle-making process, such as melting wax and pouring it into molds to forming wicks and adding fragrance or color.
Expenditures
Additional expenses to consider when planning the cost for candle making include supplies, shipping costs, advertising costs, and labor costs. To reduce these costs, you can search for wholesale suppliers of candle-making supplies, use economical shipping options (such as USPS flat rate), look into price-discounts for bulk orders, create your own advertising campaigns (like using social media), and hire skilled local workers at a reasonable cost. Additionally, if you’re selling candles online or through a store, you should factor in processing fees from payment gateways (like PayPal or credit card companies) into your budget. Lastly, it’s important to remember that all these expenses are necessary to ensure quality products that pass safety regulations and appeal to customers.
Tips for Keeping Costs Low
When it comes to keeping costs low for candle making, there are a few different techniques that you can use. First, one of the most basic tips is to always buy in bulk if possible. Buying from wholesalers or manufacturers directly can help reduce your overall costs significantly. Second, you should try to minimize waste when making candles. Using the correct sized wick for the container or mold you are using will help reduce your wax and fragrance oil usage significantly. Additionally, try to purchase materials such as containers, molds, and waxes in larger quantities. This will allow you to take advantage of discounted rates that suppliers offer on large orders. Finally, if at all possible, consider using recycled materials such as jars or cans for your projects; this will also save you a significant amount of money in comparison to purchasing new materials!
Common Mistakes To Avoid
Potential budget overruns when it comes to candle making projects can include ordering too many supplies, underestimating labor costs and not taking into account associated taxes and shipping fees.
To prevent such budget overruns in the future, consider doing the following: researching local suppliers to compare prices of necessary supplies; accurately estimating the amount of time it may take for tasks by analyzing historical data; and factoring in potential taxes or shipping fees before placing an order. Additionally, aim to save on any non-essential expenses to stay within budget. Finally, create a contingency plan ahead of time that takes into account possible deviations from original project cost estimates so that you are prepared if extra funds are needed.
Conclusion
Understanding the cost of candle making is paramount for running a profitable business that meets customer demands and expectations. By knowing what components to buy, such as wax or wicks, and where to purchase them, small business owners can maximize their profits and deliver quality products at competitive prices. Additionally, it’s important to track variable costs associated with production which can include supplies, tools and labor.
At the end of the day, keeping close watch on the project cost of candle making is necessary in order to create a sustainable business model. By managing project costs constantly, one can quickly identify discrepancies and areas of improvement in terms of savings potential. This allows entrepreneurs to stay ahead of their competition while satisfying customer needs with quality products at lower than expected prices. Exploring available resources such as online marketplaces and bulk supply stores are key ways in which businesses can optimize their costs and maximize their profits.
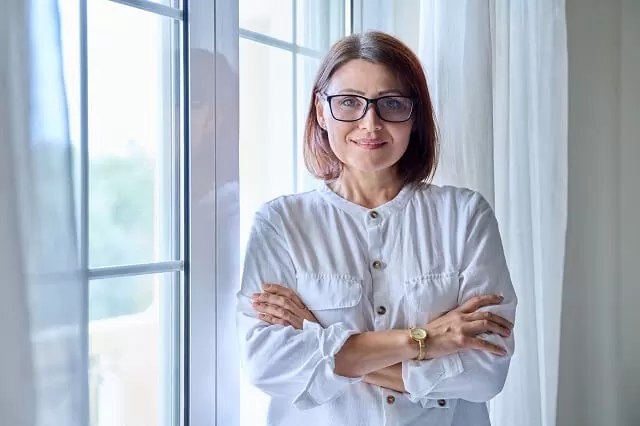
Welcome to my candle making blog! In this blog, I will be sharing my tips and tricks for making candles. I will also be sharing some of my favorite recipes.