Wax Candle Making Machine Factories Around the World
Wax candle making is a centuries-old practice that has been honed and perfected by candle makers over time. In the modern age, many wax candle making machine factories around the world employ specialized machinery to efficiently churn out mass amounts of candles. In countries like China, automated processes are in place so that a single operator can handle multiple machines and produce large quantities quickly.
India is known for its hand-crafted approach; factories often employ hundreds of workers to create intricately designed pieces using careful attention and hands-on craftsmanship. Europe has also experienced renewed interest in wax candle production, with companies offering natural scents, colors, and shapes to create more sophisticated products.
In the United States a variety of both small and large-scale operations exist, ranging from family-owned businesses to publicly traded companies who have acquired smaller business entities with unique product offerings. Many of these factories also offer an online presence as well as global distribution opportunities thanks to advances in business technology.
No matter where it is being made, all wax candle manufacturing starts with some form of combustible material such as wax or paraffin wax base materials which are melted down either manually or through automated machinery into molds or containers until they cool down into stable ingredients for use in other forms of production such as rolling or dipping processes. Companies may then introduce handmade touches such as decorations or labels if desired before finally packing their candles up for distribution across the world.
Safety First
When running a wax candle making machine factory, it is important to consider the safety aspects of production. Adhering to best practices and standards is beneficial in avoiding accidents. The most important process areas that should be kept in mind are electrical hazards, hot surfaces and materials, flammable liquids, workplace environment ergonomics and ventilation, as well as health concerns related to any chemicals used.
To mitigate potential electrical hazards, appropriate equipment protection devices and proper wiring should be installed in tamper-proof housing, and all equipment should be regularly inspected and maintained by qualified personnel. Equipment should also be placed away from wet and humid conditions to prevent corrosion or other damage. In addition to this, control components such as switches and buttons should always be marked unobstructedly for fast identification in case of an emergency or shut-down protocol.
When working with hot objects such as utensils for melting wax or hot wicks for candle finishing the utmost caution needs to be taken by operators. Proper hand wear should always be used when handling these objects as well for protecting hands from burns or abrasions. Work surfaces should also remain clean of surplus material at all times as combustible liquids or particles can cause explosions when exposed to ignition sources like candles’ flames themselves or sparks from electrical lines coming into contact with them.
Furthermore, workplace environment ergonomics must be taken into account with respects of overall illumination levels while taking frequent breaks during work hours can reduce fatigue that could lead to mistakes being made while operating machinery, potentially leading to serious harm. Machines must also feature adequate noise insulation materials without compromising ventilation quality, which helps keep air quality safe both within the factory itself but also reduces emissions released into the environment outside of it by filtering/scrubbing potentially hazardous fumes/gases like carbon dioxide given off while burning wax during production due combustion reactions taking place inside reactors connected with candle finalisation devices that could impact local air quality near production sites if not adequately checked along with health benefits associated with good indoor air quality at the workplace for workers at risk of developing long-term illnesses due long exposure periods (heart conditions & cancer linked to stress labor & poor air conditions). Finally even if chemicals do not have direct contact with human skin it is essential that a hazmat disposal protocol must still put in place just in case these would leak out accidentally during spills since this cannot be overlooked when soaps/oil bases/emulsions/pigments are employed as ingredients in recipes defining wax products manufactured within these factories for sale commercially across global markets towards consumers worldwide interested in purchasing customized offerings available inside retail outlets upon request delivered safely per governmental regulation mandating same transporters which deploy means of delivering products securely without any kind of prejudice relying on agreed logistics plans ensuring end customers are provided reliable & durable good quality product content upon delivery until point of use whereby actual consumer gets benefit out item purchased formally
The Advantages of Professional Wax Candle Making
One of the biggest advantages of professional wax candlemaking over DIY methods is the quality of the final product. With a professional machine, you can create more consistent and high-quality candles with greater consistency. This ensures that your candles look better and last longer, potentially saving you money in the long run. Since these machines are highly specialized pieces of equipment, they also have features that enable users to customize product options such as scent, color, or design elements. Additionally, factory-made wax candles often come with a longer shelf life than those made at home due to having been sealed properly in specialized containers. Professional wax candle making machines will also give you access to higher quality supplies and ingredients than what you would purchase separately at your local store or online which could help produce top-of-the-line products while reducing costs significantly.
The Impact of Automation
Automation has had a great impact on the wax candle making industry, drastically increasing production speed and efficiency. For instance, with the previously manual processes of pouring or molding candles, machines can do it far faster and better. Accurately controlled temperatures and dosages help produce colors, sizes and shapes to industry standards in as little as one tenth of the time, so companies can quickly produce candles for increased demand. Automation also reduces labor costs associated with employing workers who would be required to perform the traditional candle-making process. In addition to cost savings, automation also offers improved product quality since there is less human error involved in the process. While automation does provide many benefits for businesses in this sector, factory owners must take into account start-up costs associated with acquiring machines along with regular maintenance required to keep them running efficiently and effectively.
The Future of Wax Candle Making
The wax candle making industry is rapidly changing, and new technologies are emerging that are revolutionizing how candles are made. In the coming years, technology such as 3D printing, robotics and Artificial Intelligence will open up exciting possibilities for the industry. 3D printing can be used to create beautiful, intricate shapes and designs that would be impossible to make by hand, while robotics could automate many of the labor-intensive aspects of candle production. With AI, sophisticated algorithms can be utilized to predict and manage customer demand in order to optimize production planning and reduce waste. Additionally, advances in medical science may allow for more natural alternatives to conventional candle waxes like paraffin wax. Finally, improvements in lab testing technology mean that manufacturing processes can be refined and fine-tuned at the microscopic level for greater performance and efficiency. These technologies all have the potential to benefit the wax candle making industry significantly in the coming years.
Technical Specifications
Wax candle making machines are complex pieces of equipment employed in the production of wax candles on an industrial scale. They require a set of technical specifications to ensure efficient and successful operations. Important power requirements may include power input, overall power consumption and information related to voltage. Additionally, design specifications such as body material, frame type and safety guards must be outlined. To ensure machines remain functional over time, key components such as heating elements should also be described, including size, material type and temperature ratings. Furthermore, machines should feature adjustable spindles and various speed levels to customize production operations as desired. Finally, they must remain sturdy and safe through construction with materials like cast iron or stainless steel that offer enhanced durability and resistance against corrosive agents
Additionally, factories can consider the complexity of the machine when making their selection—some models come with highly configurable settings for advanced production optimization while others feature simpler systems for industrial beginners. It is important to note that some models may include automation features such as automatic feeding systems or automated start-up processes which could either increase efficiency or increase potential failure risks. Overall companies looking into purchasing wax candle making machines should consider any quality certifications the respective factories have obtained prior to purchase to ensure product reliability.
Machine Suppliers and Maintenance
High-end wax candle machines are often backed by manufacturer warranties and professional maintenance to ensure optimal performance even after years of use. Many suppliers also offer service plans to ensure proper operations and maintenance throughout the life of the machine, addressing any wear-and-tear issues with the included parts or components. Warranty plans can include reduced labor costs for routine checkups, so you know your machines will continue to run efficiently at all times. Additionally, many suppliers offer extras such as technical advisory services and training in quality control procedures to maximize effectiveness of your production line. These added services guarantee that even small wax candle machine factories have access to reliable and high quality machinery that meets their production requirements.
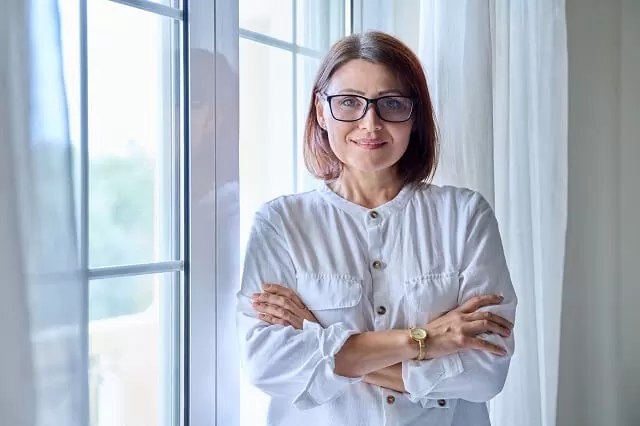
Welcome to my candle making blog! In this blog, I will be sharing my tips and tricks for making candles. I will also be sharing some of my favorite recipes.